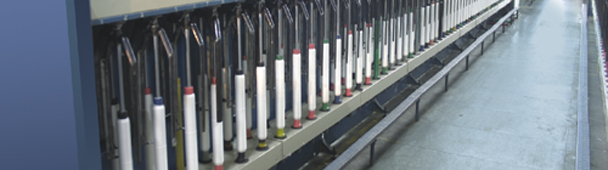
The Company operates three Spinning Units. Unit one and two are located at Kotla Kahlon, 8/9 Kilometers from Shahkot towards Sheikhupura and the third Unit is located at Kotri, Sindh. Spinning Unit 1 came into operation on July 01, 1990 and Spinning Unit # 2 was completed and came into operation in December 1994.Spinning Unit # 3 was setup at SITE Kotri and started its commercial production on January 01, 2004. Presently all the Spinning Units consist of 55,680 spindles with an accumulated capacity of 18,578,416 Kgs. of yarn converted at 20s count. Cotton as well as blended yarn is produced for the local as well as export market. The Spinning Units of the Company have received ISO 9002 certification.
Spinning Unit's Process
Spinning is the process of combination of all processes which are involved in conversion of fiber into yarn. In textile when we say spinning then we mean to say about the final process in the transformation of fiber into yarn or thread. The object of spinning and of the processes that precede it is to transform the single fibers into a cohesive and workable continuous-length yarn. In spinning process the most important thing is fiber, which is the base of thread/yarn and thread/yarn is end product of spinning department.
![]() |
Function & Operation of Spinning Section
Mixing Section
Mixing section is basically designed for the purpose of mixing different lots, because these lots are purchased from different regions and areas and contain different colors, shades and brightness ranges due to following factors, Moisture Weather Picking condition (manual or mechanical) Treatment during transportation
Objects of Mixing Hall
Cotton Opening Mixing Removing of foreign particulars like jute, and pieces of cloth etc
Blow Room
The cotton is received in blow room through condensers from the mixing section. In blow room this cotton is stocked for 12 to 16 hours for conditioning according to the temperature of blow room, in the form of layers horizontally and cut vertically which is very old method of mixing the cotton of different regions and characteristics. This process is called Sandwich Process and this way is Conventional way of mixing. All wastage extracted in the blow room is called trash.
Objects of Blow Room
Mixing Opening (tuft to tuft) Cleaning (up to 60%) Lap Formation
Processing Flow of Blow Room
The major object of different processes in blow room revolves around mixing, opening, cleaning (wastage like cottonseed or bigger particles) and lap formation. Blow room consists of following flow of machines.

Carding Section
In carding section laps are converted into sliver. In carding machines laps are feed and slivers are received as an end product in cans or boxes.
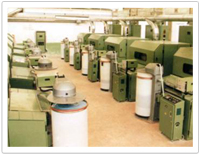
Object of Carding Section
Mixing Opening (fiber to fiber) Cleaning (about 99% of whole spinning process) Sliver Formation Drafting Elimination of Short fibers (about 1%) Sliver formation
Drawing Section
Drawing section consists of two sub-sections: i) Breaker Drawing ii) Finisher Drawing iii) iii) Drawing is a process in which different slivers are combined together to produce single sliver. Normally 8 slivers are fed behind one drawing machine and get an end product in form of single sliver in cans or boxes, which has the same weight as of single sliver. The purpose of doing this is that to create uniformity and average out the weight of each sliver. This process is also called 8/8 process
Objects of Drawing (Breaker)
Uniformity Parallelization Orientation Dust removal
Combing Section
In this process short fibers are removed and wastage of combing is called "Comber Noil" 20% of lap is extracted or removed in the form of Comber Noil during combing process. Combs are feeded in comber machine to do this process. Lap received from lap former is its input while its end product or its output is sliver, which is called here "comber sliver".
Objects of Combing Section
Removal of Short Fiber Doubling Sliver formation
Simplex Section
Finisher sliver is input of simplex machine while "roving" is its end product. Roving is a big bobbin having refined sliver (in the form of package) but thin and slim than sliver. In this process, twisting is done on roving. Here the twist per inch (TPI) is approximately 1.004. Roving is further used in "Ring Department" for making of small bobbins after that making of cones. One package normally contains 3,000 meters roving.
Objects of Simplex Machine
Drafting Twisting Package formation (conversion in roving from sliver)
Ring Section
In ring section, final spinning process starts. Here in this section roving from simplex section is turned into fine & sophisticated yarn of different counts. Pulling effect makes counts. Spindle is a smaller tapering rod, the rotation of which gives the twist and around which the thread is wound as it is twisted. These bobbins are further sent to the Auto Winder or Auto Cones department, where cones are made from them.
Objects of Ring Section
Drafting Twisting Package formation (conversion in roving from sliver)
Packing Section
Finally cones are sent to packing section where these cones are thoroughly examined under "ultra violet lights". Contamination is checked after that cones are kept in the controlled temperature of packing hall for 24 hours for conditioning. Then these cones are packed in cartoons, after wrapping in polythene bags. 24 cones are packed in one cartoon.